
This complicated steel erection was just one of the challenges faced by the design-build contractor. The process had to be repeated for 25 columns and beams down the length of the head house and the cantilevered roof. Once the head house wall and all of the Y-columns were in place, the box beams could be lifted into their three points of contact and welded into place by steel erector National Steel City. The Y-columns were shipped from Montreal in two separate pieces, put together on site and lifted as one piece. Smith says Clark/Weitz/Clarkson placed its grade beam and anchored and braced the panels so they could stand by themselves until the rest of the head house, the steel Y-columns and the box beams from fabricator ADF International could be delivered. This is the only area where we had to leave out slab-on-grade work until after we erected the steel.”īefore the box beams could be installed, the Clark/Weitz/Clarkson design-build joint venture contractor delivering the project had to erect one precast concrete wall of the head house, much like first building a load-bearing interior wall before what goes around it in a Lego house. “It’s a significant architectural element and a lot of time was spent studying the structure and how to design it, but then how to build it.
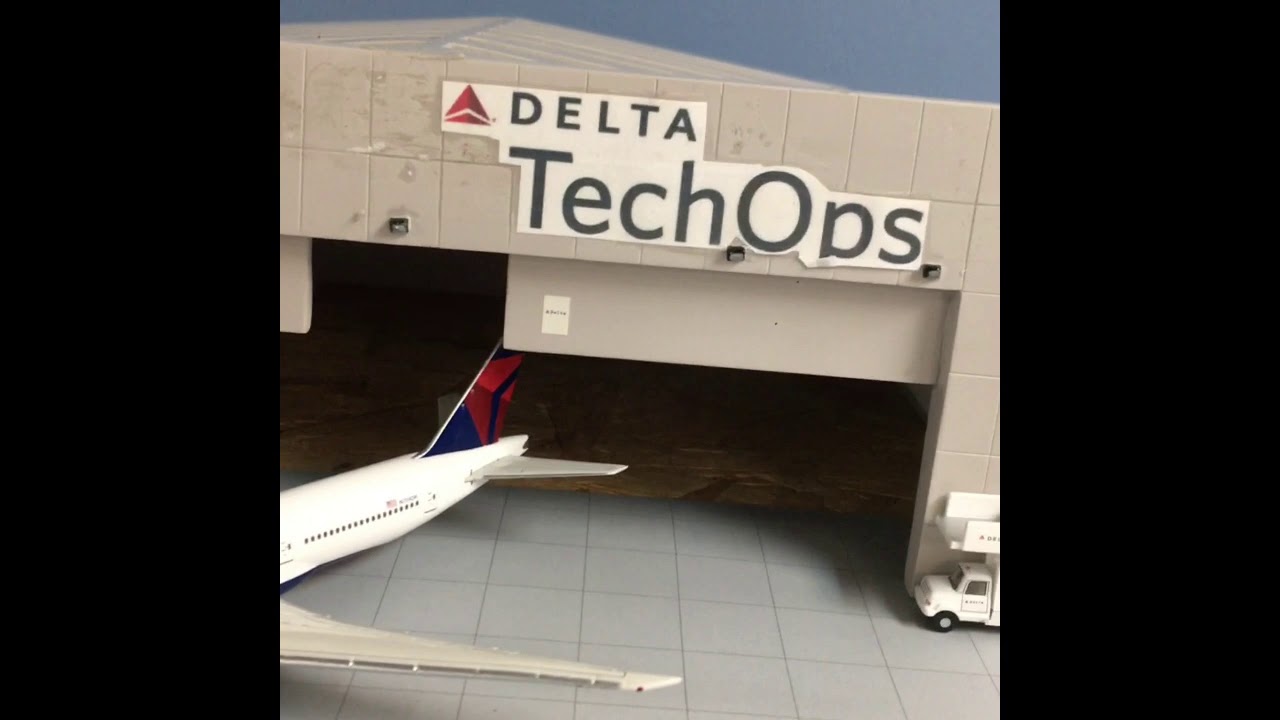
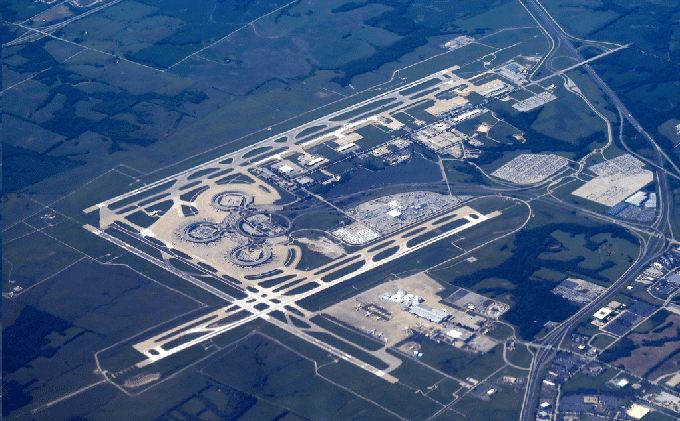
“You’ve got three points of contact, one in the back of the head house and the two points of a Y-column with a significant cantilever to cover the curbside drop-off,” says Mark Goodwin, vice president with Clark Construction Group and operations leader for the KCI Airport single terminal project. Below the 800-ft-long head house, an elevated roadway that needed its own concrete reinforcement columns complicated installation of the box beams and the steel Y-columns that hold them up.
